È tutta una faccenda di slitte, di muletti retrattili e frontali, e di picker che si muovono tra giganteschi scaffali, di lettori ottici e codici a barre, e ovviamente di braccia umane. Il deposito di un’azienda della grande distribuzione è uno snodo per le merci che arrivano, sono smistate, riassemblate, spedite. Qui siamo nel deposito centrale dell’Ikea a Piacenza – un chilometro per 200 metri di superficie, alto come un palazzo di tre piani, circa 130mila metri cubi di capacità di stoccaggio.
Per la precisione, deposito centrale Piacenza 2: un capannone che non finisce più, mentre la vecchia cascina di mattoni rossi dall’altra parte della strada sembra rimpicciolire come i palazzi di Venezia quando gli si affianca una nave da crociera.
Insomma, per rendersi conto di cosa significa la “logistica” delle merci in Italia questo è il posto adatto: per innovazione tecnologica, per volume di traffico, per la ragnatela mondiale che implica, e anche per la stratificazione del lavoro (e dei conflitti sindacali) che mette in moto.
Qui siamo al centro della rete di produttori e compratori. Senza magazzini come questo non ci sarebbero i negozi dell’Ikea, con il loro catalogo identico in tutto il mondo (ma lo stesso si potrebbe dire per ogni catena della grande distribuzione), e neppure vendite online. Per questo volevo vederlo dall’interno.
Un chilometro di scaffali
Curioso, ci si aspetta concitazione e rumore, invece tutto è silenzioso. Veicoli elettrici si muovono tra file interminabili di scaffali che salgono da terra al soffitto, o tra le zone di carico e scarico, le “baie”. Il punto è organizzare in modo funzionale il flusso della merce, spiega Andrea Colzani, amministratore delegato della logistica dell’Ikea, mentre mi porge le scarpe antinfortunio (obbligatorie per entrare nel deposito): è lui a guidare la visita.
Proviamo a ricostruire i passaggi. Piacenza è in posizione strategica, al centro della rete di trasporti. Qui siamo accanto all’autostrada Milano-Napoli (A1) e alla Torino-Brescia (E70), quindi a breve distanza dai porti di Genova e di La Spezia.
Le merci arrivano qui da fabbricanti più o meno lontani (l’Italia è il terzo fornitore dell’Ikea al livello globale, dopo la Cina e Polonia). Un armadio in scatola di montaggio, un frigorifero, un set di bicchieri o di lenzuola, fa quasi lo stesso: sono sempre scatoloni poggiati su piattaforme (i pallet), ben imballati con il cellophane e targati con codici a barre. Avranno viaggiato per mare in un container che sbarca a Genova o a La Spezia o a Ravenna, o forse hanno attraversato l’Europa in un vagone ferroviario o su un Tir, ma alla fine c’è sempre un camion che entra nel piazzale di questo deposito, si accosta a retromarcia a uno dei 164 varchi e apre i portelloni.
Le braccia umane contano ancora, e anche la rapidità
A quel punto intervengono gli scaricatori, uomini (e alcune donne) su veicoli elettrici (detti anche muletti) con le forche elevatrici. Ci sono quelli frontali che avanzano, sollevano i pallet e li tirano via, o quelli retrattili – vanno all’indietro e si muovono meglio tra i corridoi.
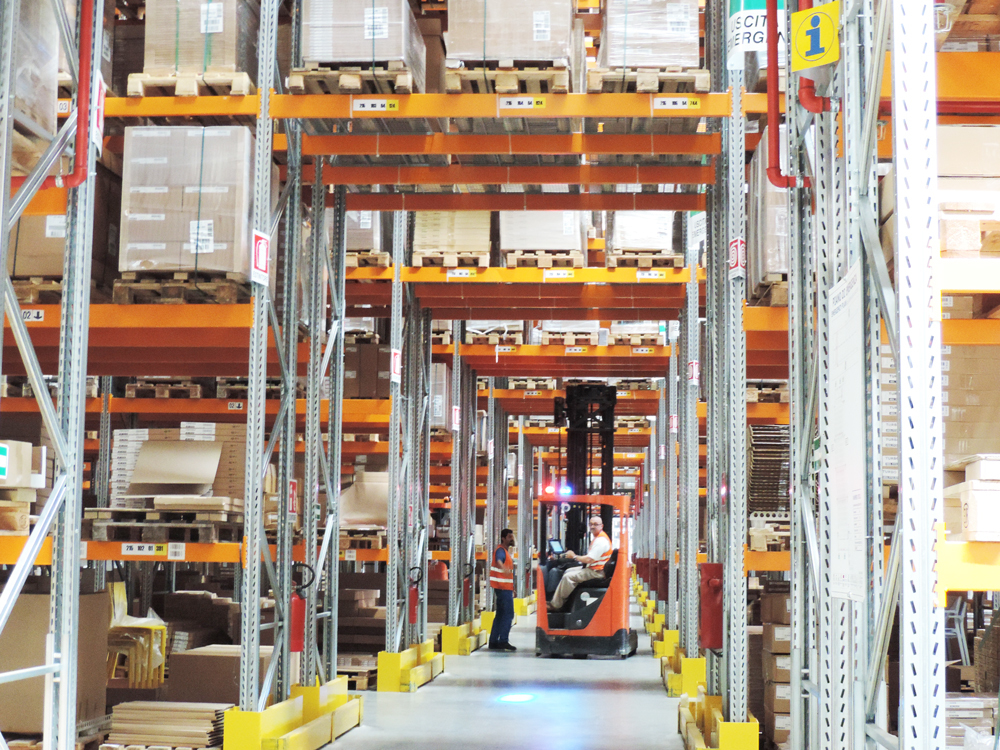
Ancora imballata, la merce può finire nella zona di stoccaggio in attesa di ripartire verso i negozi dell’Ikea in Italia o in Svizzera, in Croazia, in Romania, in Grecia, in Turchia, a Cipro, in Egitto, fino alla penisola arabica, “a volte facciamo un backup per la Spagna e il Marocco”.
Sono i moduli centrali del deposito, silos completamente automatizzati: rulliere, montacarichi, e il robot (pare una specie di gru gialla) che solleva il pallet, scorre lungo gli scaffali, lo deposita. Oppure lo va a cercare e lo mette su un altro nastro a rulli. Ci sono dieci di questi robot. Se di giorno i pallet sono stati immagazzinati in fretta, di notte il robot li riordina in modo che quelli uguali stiano di fronte. Ovviamente da qualche parte c’è un computer che sa cosa c’è in magazzino e dove, cosa entra o esce e quando.
Non tutto è così automatizzato, si intende. Nei primi tre moduli del deposito, che gestiscono la merce diretta al cliente finale, gli elevatori meccanici sono solo un supporto: le braccia umane contano ancora, e anche la rapidità. Gli addetti si muovono sulle slitte, piccoli veicoli con una sorta di carrello. L’addetto (il picker) ha davanti uno schermo, il computer gli dice cosa deve cercare. La slitta scivola tra scaffali dove gli imballaggi aperti sono sistemati ai piani più bassi. L’addetto tira su (o giù) gli oggetti disparati che compongono una singola ordinazione e li mette nel carrello che poi porta alla “baia” di imballaggio.
Qui ci sono dei banconi dove altri addetti assemblano l’ordinazione in uno scatolone che infine sarà affidato al corriere per la consegna (al domicilio del cliente, o presso un negozio della catena).
“L’organizzazione del magazzino segue le linee guida della casa madre, ma abbiamo ampia autonomia per sperimentare le nostre soluzioni, e innovare”, dice Colzani (e aggiunge con un certo orgoglio: “Solo otto depositi dell’Ikea al mondo hanno questa autonomia”, quelli dell’Europa del sud).
Dopo il terremoto che ha colpito l’Emilia nel 2012, qui le scaffalature sono state rifatte con criteri antisismici
Indica una macchina che ottimizza la dimensione degli scatoloni, per far entrare il maggior numero di cose in meno spazio: “L’abbiamo ripresa da Lione, e il risparmio è consistente: se il test sarà positivo l’adotteranno in altri depositi”. Poi c’è lo studio per far entrare più merci imballate in un singolo camion: qui hanno creato piattaforme di cartone compresso, con tanto di piedini, che pesano meno e occupano meno spazio del pallet di legno. Colzani parla di innovazione e di best practices, “migliori pratiche”: quando un magazzino ha messo a punto una buona soluzione, diventa un esempio per gli altri che la copiano.
Il tetto fotovoltaico
Tra le innovazioni, qui c’è il tetto, coperto da più di 66mila pannelli in silicio. È uno dei più grandi impianti fotovoltaici privati in Italia, 6,98 megawatt di potenza installata, copre l’intero consumo annuale del deposito e immette qualcosa nella rete.
“Abbiamo costruito noi il deposito, tra il 2004 e il 2007, così abbiamo potuto progettare per diminuire l’impatto ambientale”, spiega Colzani. Per esempio, i finestroni che si aprono in alto lungo tutto il capannone fanno entrare molta luce; un sistema di sensori misura la luminosità all’interno e comanda l’accensione delle luci, solo quelle necessarie (in un giorno assolato ne vedo meno di una su due, a file alterne). I veicoli interni hanno batterie elettriche. Il 95 per cento dei materiali di scarto – legno, cartone, plastiche degli imballaggi – va nella raccolta differenziata. I pallet di legno sono aggiustati e riutilizzati finché possibile, poi finiranno all’azienda municipalizzata per essere smaltiti.
Poi ci sono le misure di sicurezza. Dopo il terremoto che ha colpito l’Emilia nel 2012, qui le scaffalature sono state rifatte con criteri antisismici. Gli ispettori della sicurezza percorrono ogni giorno il deposito per controllare che ogni scaffale, piede, traversa sia a posto. Luci blu ti avvertono che dietro l’angolo c’è un muletto in movimento. Nel deposito ci sono defibrillatori, sistema antincendio, controllo dell’aria nei container (per la sicurezza dei co-worker, leggo nel materiale illustrativo fornito da Ikea: termine anglofono per indicare i dipendenti delle aziende esterne).
Co-worker? L’intera divisione della distribuzione dell’Ikea (inclusi impiegati e dirigenti) occupa 300 dipendenti, quasi tutti a Piacenza. Ma gran parte degli addetti che vedo sfrecciare sulle slitte nel deposito dell’Ikea sono esterni: ci sono tra i 350 e i 400 dipendenti di aziende in appalto (si riconoscono dalle pettorine arancione), su una settantina di dipendenti interni addetti al magazzino (maglia blu). Come ogni azienda della logistica, l’Ikea “esternalizza” molto lavoro, il facchinaggio, le pulizie. E il trasporto vero e proprio, affidato a corrieri.
Da questo deposito parte un centinaio di camion al giorno; tra arrivi e partenze si arriva a circa 300 giornalieri. A poche centinaia di metri da qui, dall’altro deposito dell’Ikea a Piacenza (che in effetti è il primo, aperto nel 1999) ne conta in media un centinaio – di più tra settembre e fine anno, i mesi più intensi per la grande distribuzione.
La fatica umana
Cosa significa un deposito come questo, in termini di lavoro umano? Perché l’automazione è alta, ma non deve ingannare: “movimentare merci” resta un lavoro faticoso. Certo, il deposito centrale Piacenza 2 è all’avanguardia, questo lo riconoscono anche i sindacati. “È un’azienda che tiene all’immagine, cura l’ambiente di lavoro, ci badano”, mi dice Michele De Rose, della Filt-Cgil di Piacenza: “Ma ci sono operazioni ripetitive, manuali. C’è fatica, altroché”.
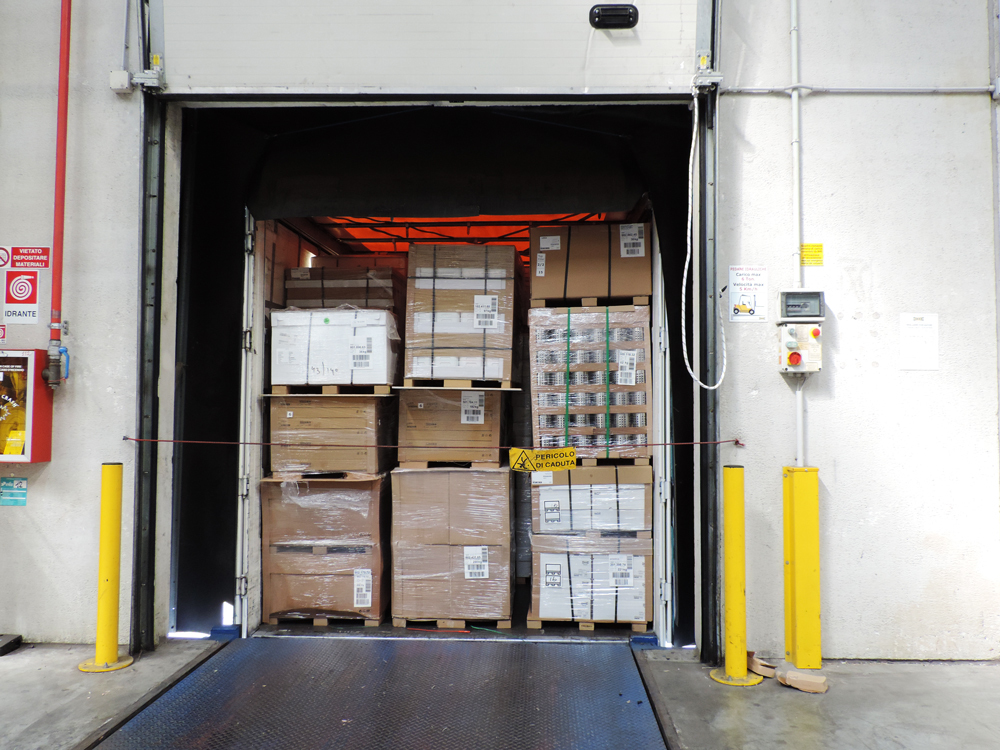
“Ti dicono: dovete scaricare un container in tre ore e mezza, un camion in meno di un’ora”, mi dice Bruno Scagnelli, oggi operatore del SiCobas a Piacenza, fino a un anno fa facchino all’Ikea – cioè, presso una delle cooperative a cui l’azienda appalta la movimentazione delle merci nel suo deposito.
Come nei magazzini dei corrieri, infatti, anche qui le aziende appaltatrici sono cooperative. E anche qui nel passaggio dal “committente” (Ikea) al “fornitore” di servizi (la cooperativa) il rispetto dei contratti diventa aleatorio e i diritti dei lavoratori entrano in una zona grigia. O almeno, questa era la situazione quando proprio a Ikea è scoppiata una delle prime battaglie sindacali della logistica.
La prima vertenza qui risale all’autunno 2012. Protagonista il SiCobas, che rivendicava il rispetto del contratto nazionale disatteso dalle cooperative. “I dipendenti hanno un contratto a tempo indeterminato. Ma le cooperative praticavano una sorta di lavoro a chiamata”, spiega Edoardo Pietrantoni, coordinatore del SiCobas: nei momenti di picco era un superlavoro, nei momenti di bassa ti chiamavano per poche ore, “finivi con una busta paga di 500 o 600 euro”.
Non è un segreto: il facchinaggio è appaltato all’esterno proprio per gestire i cicli del lavoro, e avere a disposizione più o meno operai a seconda delle necessità. Per di più, per le stesse mansioni, per alcuni era applicato il contratto dei trasporti-logistica, per altri il “multiservizi”, con salari più bassi. “In sostanza rubavano sulla busta paga”, mi dice Scagnelli nella sede del SiCobas, nel centro di Piacenza.
Sta di fatto che la vertenza si è scaldata. La “controparte” era un consorzio (Cgs) che a sua volta subappaltava il lavoro a tre cooperative, ma è ovvio che l’Ikea fosse parte in causa. Le richieste dei lavoratori infine sono state in buona sostanza accolte: era l’inizio del 2013, Pietrantoni parla di “una fase di dialogo”.
Negli uffici del deposito dell’Ikea, Colzani riconosce che la situazione era “molto poco chiara”, e che non era nel loro interesse (ogni fermata del lavoro significa ritardi e perdite). Così l’azienda ha cambiato strategia: “Abbiamo deciso di eliminare il subappalto”. Dal settembre 2013 Ikea appalta il lavoro a due cooperative – la Coop San Martino nel deposito centrale Piacenza 2, Sigest nell’altro: “Controlliamo che rispettino il contratto di lavoro, facciamo controlli sulle buste paga. Abbiamo anche chiesto una certificazione a un gruppo dell’università di Pavia”.
Chiedo se finirà come ad Amazon dove i dipendenti sono incoraggiati a pugnalarsi alle spalle
Questo non ha impedito una scia di conflitti nel 2014 (tra il SiCobas e la Cooperativa San Martino, con una complicata vicenda di lavoratori vicini al sindacato autonomo estromessi: Scagnelli è uno di loro). I lavoratori incontrati presso il SiCobas continuano a parlare di ritmi incalzanti – “a volte ti trovi a scaricare un container da solo”. Ma siamo lontano da quel sistema di “caporalato” di fatto visto in altre aziende della logistica.
Comunque sia, oggi, alla logistica dell’Ikea non ci sono vertenze aperte. I sindacati confederali stanno negoziando un nuovo accordo, che però riguarda i soli dipendenti diretti.
In fondo, lo spartiacque tra confederali e sindacato autonomo, almeno nella logistica, è proprio questo: i primi rappresentano più che altro i dipendenti diretti della grande azienda; i sindacati di base invece hanno guadagnato credito presso i facchini delle cooperative in appalto, più vulnerabili, in maggioranza immigrati: nel momento più caldo della vertenza, a Piacenza, oltre metà di chi lavorava nel deposito era iscritto al SiCobas.
La Filt-Cgil, per recuperare terreno, vuole definire un “protocollo” con standard economici e di qualità per gli appalti nel facchinaggio, che ricalca una legge regionale dell’Emilia-Romagna: spera di farne un modello per altre aziende della logistica.
I dirigenti dell’Ikea sembrano favorevoli: “Vogliamo che le aziende a cui diamo appalti siano sane, senza infiltrazioni mafiose, rispettino contratti e buste paga”, dice Andrea Colzani. Gli appalti dell’Ikea sono tra i più cari del piacentino, sottolinea: “Come tutti lavoriamo a ridurre i costi, ma non sul personale. Meglio lavorare su efficienza e flussi logistici”.
Già, la competizione si gioca sulla rapidità. L’Ikea per esempio ha negoziato con l’agenzia delle dogane un “corridoio controllato doganale”, in vigore da maggio. In pratica, i container che sbarcano nei porti italiani diretti ai suoi depositi piacentini passano dalla nave al trasportatore autorizzato, sigillati e tracciati con gps, e sono sdoganati direttamente a Piacenza.
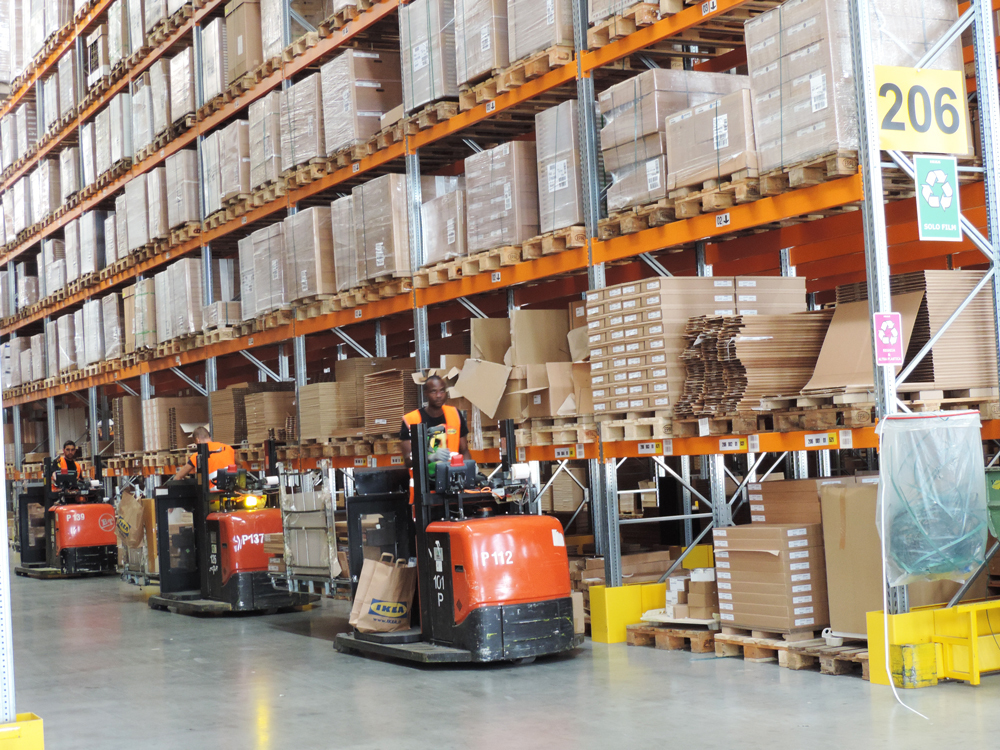
È il primo accordo del genere in Italia, una sorta di test; ci sono voluti tre anni di studi e colloqui per metterlo a punto. Per le dogane, il vantaggio è decongestionare i porti; per l’azienda ridurre i tempi del flusso di merci: “Ha permesso di tagliare di almeno otto giorni la sosta in banchina, un bel risparmio”.
Il concorso delle “buone idee”
“Facciamo di tutto per stimolare le innovazioni”, mi dicono Andrea Colzani e la responsabile della comunicazione dell’Ikea, Ornella Marangon. Siamo nella mensa aziendale, annessa al deposito: arredamento di legno chiaro, self service (questo è un servizio interno, niente appalti). Ogni giorno ci mangiano circa 300 persone, facchini e impiegati, dipendenti interni e degli appalti, camionisti, e a quanto vedo anche i dirigenti. Il business nei depositi dell’Ikea a Piacenza è aumentato anche se globalmente le vendite si sono contratte, dice Colzani, “perché abbiamo saputo migliorare i processi logistici”.
“Siamo sempre alla ricerca di migliorie”, tutti i dipendenti “sono incoraggiati a fare suggerimenti postando idee sul social network interno”, aggiunge Marangon.
Il suggerimento che si dimostra più efficace è premiato, “anche piccole innovazioni”: cita quella di programmare le stampanti per usare il foglio fronte-retro, di default, risparmiando carta. Si intuisce una certa competizione (virtuosa?). Mi parlano di un’indagine interna sul clima di lavoro nell’Ikea: il polo di Piacenza ha avuto un indice ottimo. Citando un’inchiesta del New York Times, chiedo se non finirà come ad Amazon, dove i dipendenti sono incoraggiati a pugnalarsi alle spalle. Sorrisi. No, certo che no. “Ma qui si lavora sempre per migliorare”.
Internazionale pubblica ogni settimana una pagina di lettere. Ci piacerebbe sapere cosa pensi di questo articolo. Scrivici a: posta@internazionale.it